Retaining rings are typically classified as either internal or external, each with unique characteristics and applications. Internal retaining rings are installed within a bore, while external retaining rings fit over a shaft. Understanding the differences between these two types is crucial for selecting the appropriate retaining ring for specific engineering applications.
Internal retaining rings are designed to prevent axial movement of components within a bore. They are typically made of spring steel and are available in various shapes, including C-rings, E-rings, and spiral rings. Internal retaining rings are commonly used in automotive, aerospace, and industrial machinery.
Retaining Rings: An Overview: Retaining Rings Are Typically Classified As Either
Retaining rings are crucial mechanical components that secure and position other components in assemblies. They play a vital role in various industries, including automotive, aerospace, and manufacturing.
Retaining Rings Types
Retaining rings are primarily classified into two types based on their design and application:
- Internal Retaining Rings: These rings fit inside a groove on the shaft, securing components in an axial direction.
- External Retaining Rings: These rings fit outside a groove on the shaft, securing components in a radial direction.
Type | Description |
---|---|
Internal | Fits inside a groove on the shaft |
External | Fits outside a groove on the shaft |
Internal vs. External Retaining Rings, Retaining rings are typically classified as either
Internal and external retaining rings serve different purposes and have distinct advantages:
Internal Retaining Rings
- Prevent axial movement of components
- Compact and space-saving
- Can be installed in blind holes
External Retaining Rings
- Prevent radial movement of components
- Easy to assemble and disassemble
- Can be used on shafts with shoulders or steps
Materials and Manufacturing Processes
Retaining rings are typically made from high-strength materials to withstand operational stresses:
- Steel: Common choice for high strength and durability
- Stainless Steel: Corrosion-resistant and suitable for harsh environments
- Spring Steel: Provides flexibility and high resilience
Manufacturing processes for retaining rings include:
- Stamping: Most common method, involves punching rings from sheet metal
- Rolling: Creates rings by rolling wire or strip material
- Wire Forming: Shapes wire into rings using specialized machines
Design Considerations
Retaining rings should be designed considering various factors:
- Groove Dimensions: Groove width, depth, and chamfer are critical for proper fit
- Material Strength: Rings must withstand loads and stresses without deformation
- Operating Environment: Consider factors like temperature, vibration, and corrosion
Proper design ensures optimal performance and longevity of retaining rings.
Applications and Industries
Retaining rings find applications in a wide range of industries:
- Automotive: Secure bearings, gears, and other components in engines and transmissions
- Aerospace: Hold critical components in aircraft engines and landing gear
- Manufacturing: Secure bearings, shafts, and other parts in machinery
- Medical: Used in surgical instruments and medical devices
Answers to Common Questions
What are the key differences between internal and external retaining rings?
Internal retaining rings are installed within a bore, while external retaining rings fit over a shaft. Internal retaining rings prevent axial movement of components, while external retaining rings prevent radial movement.
What are the advantages of using internal retaining rings?
Internal retaining rings are easy to install and remove, require less space than external retaining rings, and provide a secure hold on components.
What are the applications of external retaining rings?
External retaining rings are used in applications where radial movement needs to be prevented, such as on shafts, bearings, and gears.
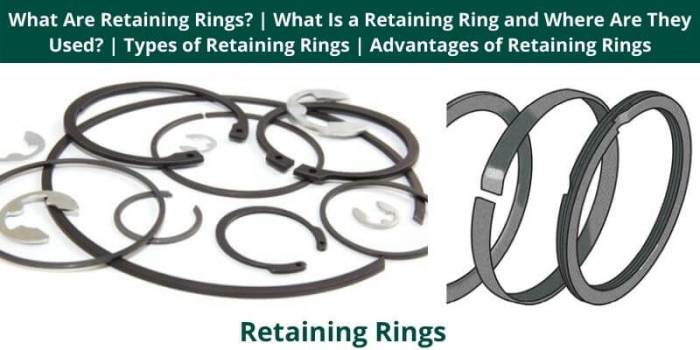
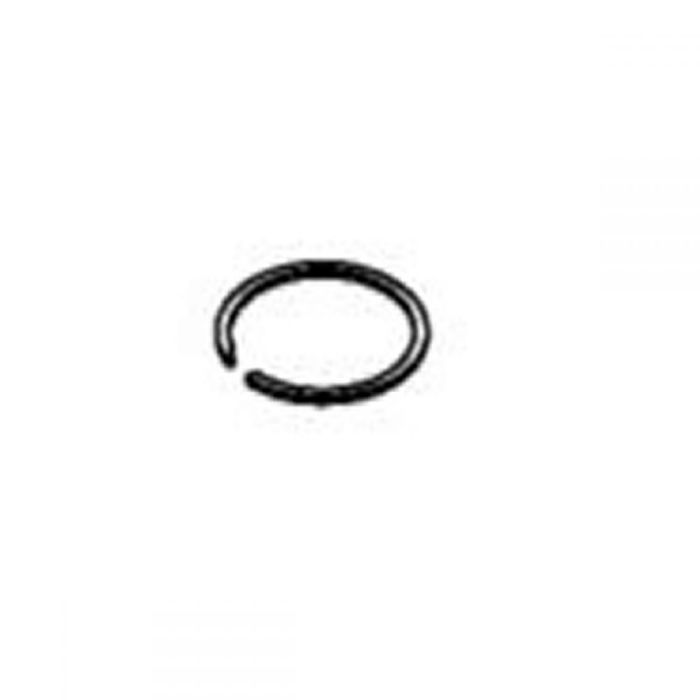
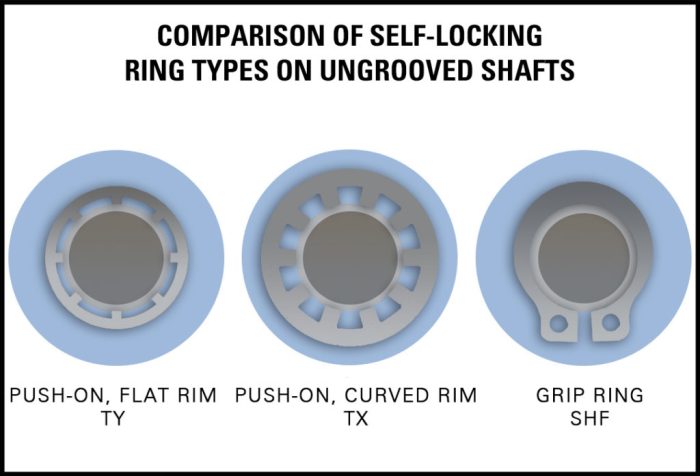